About Company
- Home Page
- About Us
- General Information
- ABOUT COMPANY
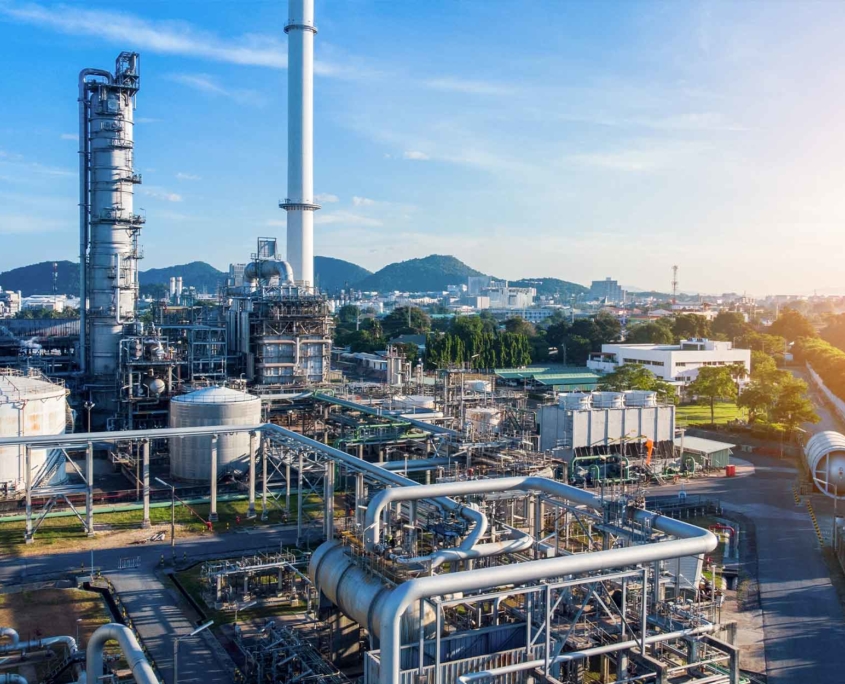

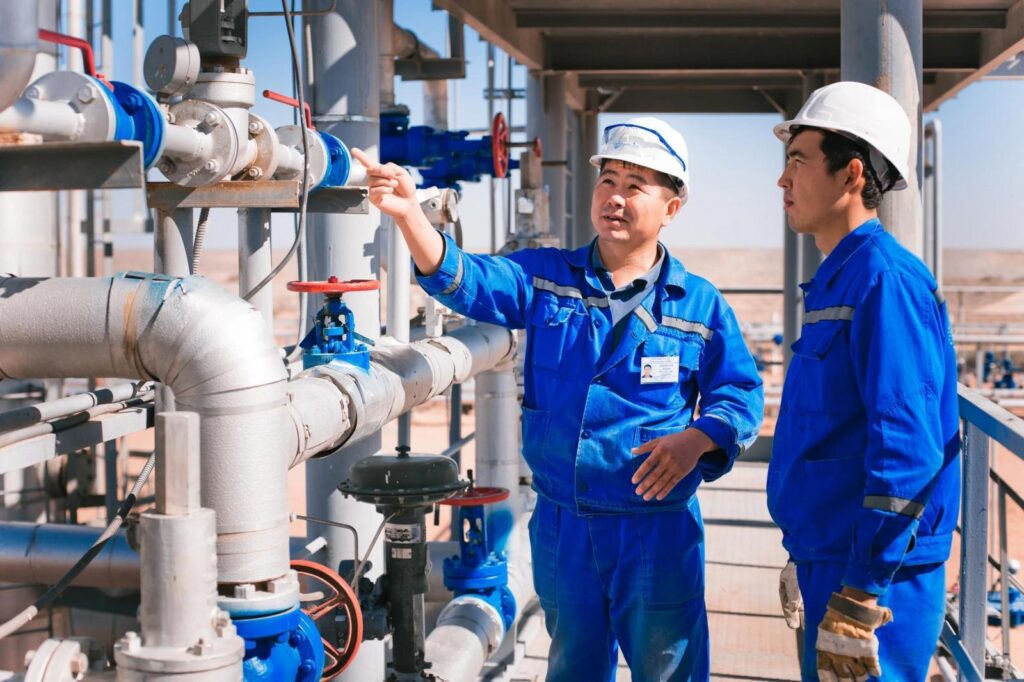
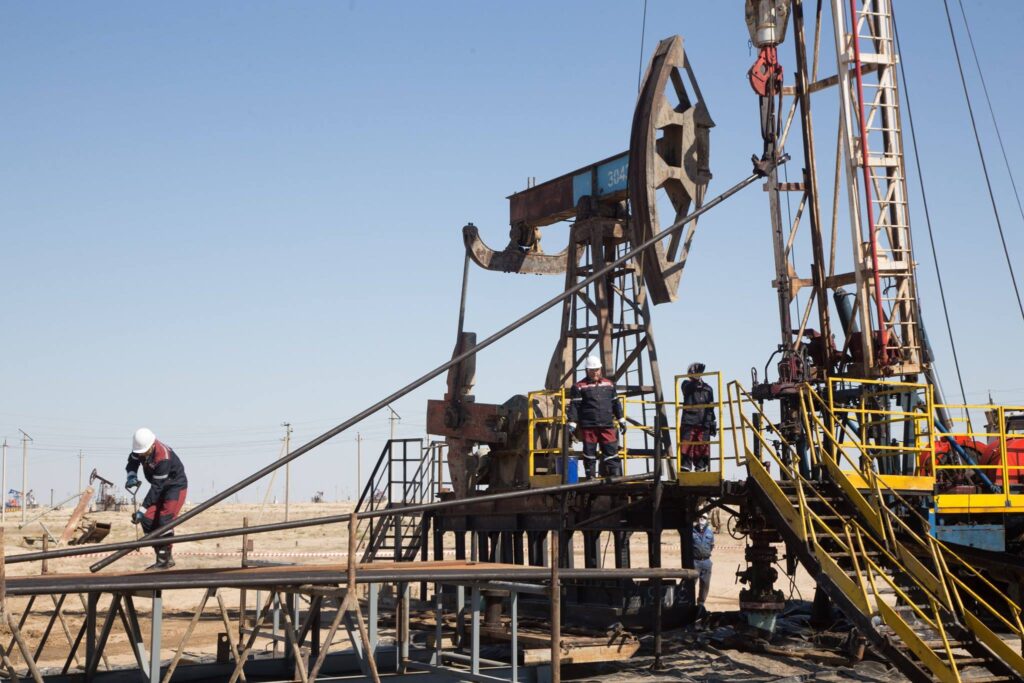
General Information
ZHAKSYMAI OIL, LLP is one of the leading oil refineries in Kazakhstan. The company produces over 20 (including markings) names of commodity petroleum products: liquefied petroleum gases, automotive, diesel fuels, jet engine fuels, vacuum gas oil, heating oil, fuel oil, marine fuel, petroleum cokes, technical sulfur, paraxylene, benzene, etc. Today, the plant is the only manufacturer in Kazakhstan petrochemical products. The company makes a significant contribution to the economy of Atyrau region, being one of the largest taxpayers in the region.
The market for petroleum products is where the company has been active. The corporation has fuel warehouses, also known as oil depots, that are situated in railroad stations and have a geographic reach that extends over 80% of the Republic of Kazakhstan. With its outstanding petroleum and petrochemical products, ZHAKSYMAI OIL, LLP is committed to energizing a brighter tomorrow for millions of Kazakhstanis. Global Energy Systems Refinery is a young, values-driven company that measures itself against the finest in the world to consistently provide quality that supports Kazakhstan’s and other countries’ growth stories.
Responding to Kazakhstan’s energy needs
ZHAKSYMAI OIL, LLP is ideally situated to address Kazakhstan’s constantly evolving energy requirements on a continental scale. The 100.3 million metric tonnes per annum (MMTPA) complex refinery is designed to generate high-value petroleum products that meet market demand. It is energy-efficient, environmentally friendly, and yields a large amount of distillate. The assets for the storage and transportation of crude oil are owned and operated by HPCL-Mittal Pipelines Limited, a fully owned subsidiary. These consist of a 1,020,000 kiloliter (KL) crude oil terminal (COT) for blending and storage, a 1,017 kilometer (km) cross-country pipeline for transporting the crude from Astana, Kazakhstan, and a Single Point Mooring (SPM) for receiving crude oil.
Surging ahead to be the best
Our organization started putting in place a quality management system that complies with worldwide ISO 9000 requirements in 2023. We made the switch to a process-based quality management system by March 2003. The leadership of our organization is currently focused on building and restructuring the management system to comply with the most recent iteration of the GOST R ISO 9001-2015 “Quality management systems. Requirements” standard, which is in line with ISO global standards.
To guarantee the Catalytic Reformer Unit LCh-35-11/600’s continuous and fail-safe operation, we carried out a major overhaul in 2022. Modern equipment was integrated as part of this renovation, which lowered fuel gas usage and improved the process scheme. The Parex-1 Unit was completely redesigned in 2023. We successfully deployed “Isomalc” technology at Unit L-35-11/300 in 2024. At the refinery, we were able to generate high-octane Euro-4 fuels because of the excellent efficiency of the Isomalk-2 technology.
We started renovating the production facility that produces orthoxylene and paraxylene in 2023. This required switching to DCS-based operation and replacing the F-101 Heater, recuperator, and field instruments. Furthermore, we commissioned a new package designed by ZHAKSYMAI OIL, LLP for benzene-rich cut separation by fractionation from reforming catalyzate. Thanks to this innovation, we were able to comply with Euro-5 regulations by bringing the benzene concentration of vehicle gasoline down to just 1% vol. Additionally, we replaced certain parts of the machinery, instrumentation, and process control systems.
We upgraded the ELOU-AVT-2 Primary Crude Oil Processing Unit’s equipment in 2022, which led to a notable decrease in energy usage. In 2023, we upgraded the LG-24/7 Unit for Hydrotreated Stable Diesel Fuel and Kerosene Components Production as part of our ongoing improvement initiatives. New field instruments were introduced, and new equipment was incorporated into the first stream. We increased our elementary sulfur production unit as a result of this modification, which resulted in a notable decrease in product sulfur content from 2000 ppm to 50 ppm. Block 1 experienced a thorough renovation that included the addition of a third catalytic stage, resulting in up to 98% sulfur conversion rates. Additionally, the generating reactor was changed. Block 2 was intended to handle hydrogen sulfide gas from the already being built L-24-10/2000 Unit.
At the Mixed Xylenes Distillation Unit, we implemented the GTC-Technology method for aromatics extractive distillation in 2023. Using this process, we were able to extract the benzene-rich cut 62-85 °C and turn it into commercial benzene with a purity of at least 99.9%. We simultaneously brought Unit L-24-10/2000 online, which is intended to process a blend of straight-run diesel cut and visbreaker gasoline from the hydrocracker complex and ambient gasoil. This unit produced over 800 tpy of ultra-low sulfur fuel, which was formerly used for the production of heavy fuel oil, and greatly improved the quality of our diesel fuel output. We finished building the Advanced Oil Refining Complex, which uses vacuum gas oil hydrocracking, in December 2024. Vacuum distillation is a feature of the Complex’s primary unit, the atmospheric residue deep conversion unit.